Silicon Carbide Seals
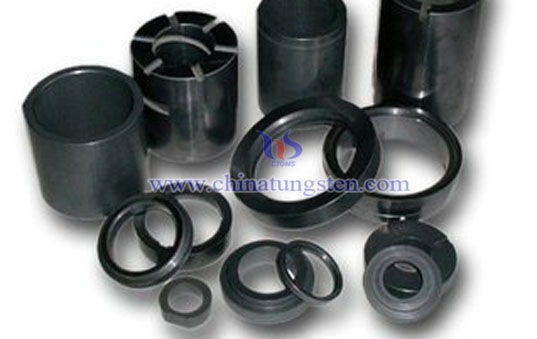
Silicon carbide is the ideal sealing material. It has good corrosion resistance, higher mechanical intensity, excellent resisting wear ability and high temperature, good self-lubricity and making-group, low friction factor, good heat-conduction and so on. Therefore, silicon carbide seals also possess the property of excellent resistant-corrosion, high mechanical strength, high thermal conductivity and good self-lubrication. Silicon carbide seals are widely used in many different industries, including spacecraft, machinery, metallurgy, printing and dyeing, foodstuff, pharmaceutical, auto industry etc.
Why make from silicon carbide?
Silicon carbide is a more expensive seals material with the carbon, but it is often used in more demanding applications. For example, blistering is a critical concern with carbon bearing materials. Strangely, the reason why blistering sometimes occurs is not known for certain. The most popular explanation is that a certain amount of material becomes absorbed in the carbon substrate and expands because of frictional heat, thus creating a crater in the seals face. Blistering is most often found in applications involving heavy oils. In some cases, the use of silicon carbide as a mating surface will eliminate a blistering problem.
Silicon Carbide (SiC) physical property |
||||||
Technical parameter |
Unit |
RBSiC |
SSiC |
Sic+C |
Ssic+C |
Qssic+C |
Content of Sic |
% |
≥90 |
≥98 |
≥85 |
≥92 |
≥90 |
Free Si |
% |
≤10 |
≤1 |
≤12 |
/ |
/ |
Elastic Modulus |
GPa |
≥400 |
≥410 |
≥350 |
≥360 |
≥180 |
Temperature |
°C |
1300 |
1400 |
1300 |
1400 |
1400 |
Hardness |
HS |
110 |
115 |
≥105 |
≥110 |
≥100 |
Porosity Rate |
% |
<0.3 |
<0.2 |
<0.5 |
<0.5 |
<5 |
Density |
g/cm3 |
3.00~3.05 |
>3.10 |
2.69-2.90 |
2.70-3.0 |
2.65 |
Compressive Strength |
MPa |
>2200 |
>2500 |
>1400 |
>1600 |
>800 |
Fractural Strength |
MPa |
>350 |
>380 |
>150 |
>160 |
>100 |
Coefficient of Heat Expansion |
10-6/°C |
4 |
4.2 |
3.50 |
3.00 |
2.50 |