Silicon Carbide Seal Ring Manufacturing Process
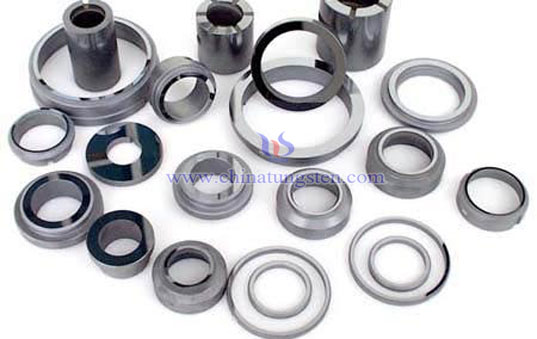
Silicon carbide is highly covalent non-oxide material, Si-C bond between ionic only 14%. High stability of the Si-C bond SiC aspect impart a high melting point and hardness, and chemical inertness, on the other hand so that the diffusion rate of sintering relatively low. Only in the participation of the additive, the control purity and fineness of the raw material, or to make it by pressure sintering at a particular atmosphere. Silicon carbide seal ring manufacturing processes mainly: material handling - mixing - Forming - Sintering - Grinding and polishing - assembly.
Material handling process: surface area SiC raw material different ball milling time and the ratio of the measurement.
Molding Process: dry pressing and isostatic pressing process, the former suitable for simple shapes, larger quantities of products, which is a small amount of a single piece, the shape of the product is more suitable for complex, and silicon carbide seal ring which by isostatic pressing has better density and performance than dry pressing products.
Hot pressing process: pressing and sintering process called hot pressing process together. Pressureless sintering process: silicon carbide biscuit after molding under protective gas in a furnace called a non-pressure sintering temperature sintering.
Grinding and polishing: Silicon carbide is a hard and brittle ceramic materials, in order to prevent product chipping off angle, it is necessary for the acute treatment pour blunt. Only choose the right size abrasive and strictly control the grinding rate and tooling necessary conditions in order to reach the surface roughness of the seal faces.
Assembly process: silicon carbide seal rings in addition to the overall structure, but also a large number of sets of inserts using thermal structure, and silicon carbide seal ring inserts the ring seat majority titanium alloy materials.